航空发动机的涡轮和压气机每一级上都有很多叶片,在运行过程中,叶片表面会积聚灰尘、沙子、空气中的污染物颗粒或烟灰、盐雾、昆虫和鸟类的残躯等,导致气动外形被改变、发动机效率降低(油耗增加)的同时,也会造成叶片腐蚀、加速老化,给发动机带来故障隐患。 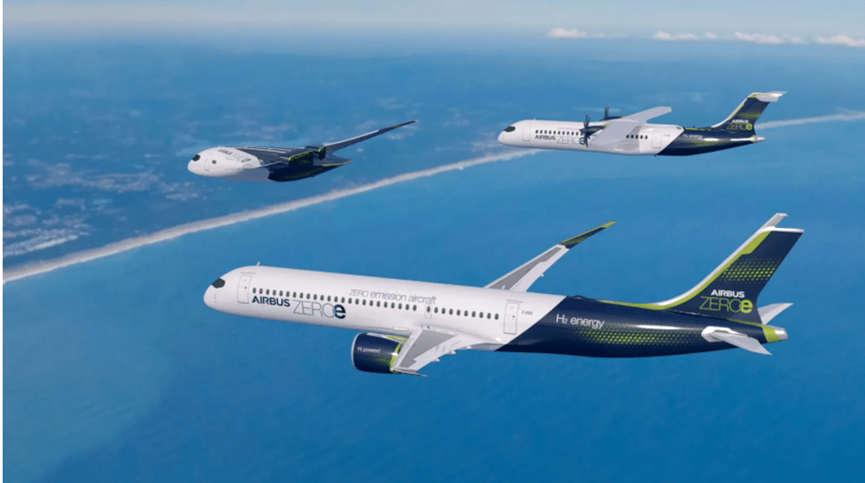
图1.运行中航空飞机 发动机燃烧燃料在更高温度下运行,这可能导致发动机过早维护。每节省一公斤燃料,就可以减少 3.15 公斤的二氧化碳排放。定期清洗减少高达 1.5% 的燃料消耗 燃气轮机用户遇到的性能降低的最常见原因之一是结垢。结垢积碳通常占运行性能损失的 70% 以上。同时发动机工作时,因发动机燃烧不充分在旋流槽、中心孔、喷嘴内腔壁上及油滤上会形成结焦积碳,某些污染物,例如污垢、灰尘、油、花粉和盐,往往会粘附在翼型表面,导致翼型进气角和翼型形状发生变化,并增加表面粗糙度导致翼型喉部孔径变窄 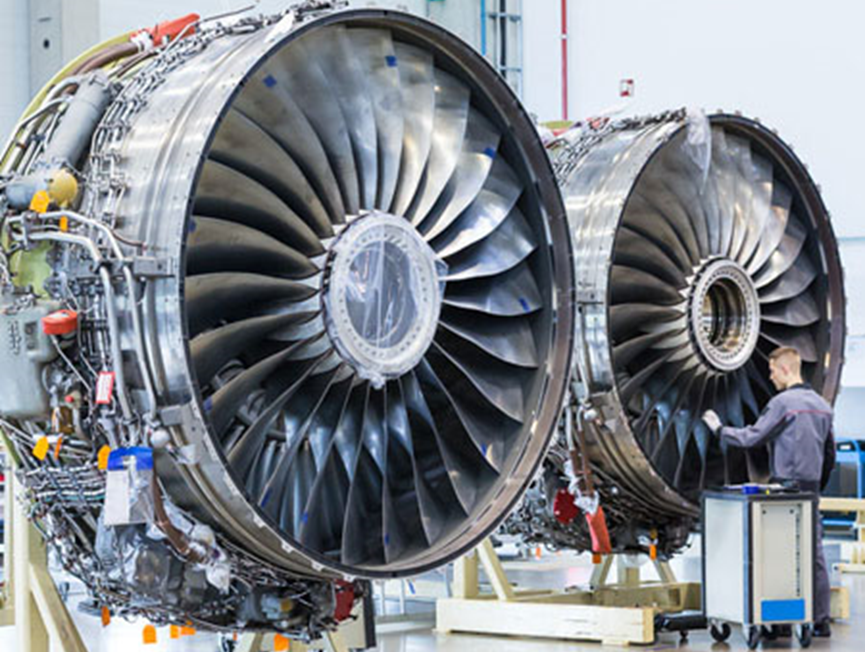
图2.检修中的航空发动机 航天航空发动机检修清洗大多以传统的喷洒去离子水、加热水和雾化/喷雾、浸没、化学清洗剂泡洗、高温烧结、超声波清洗技术为主。清洗剂泡洗是利用化学药剂浸泡积炭部件,通过化学反应使得积炭脱落,该方法主要针对叶片等小零件;高温烧结主要针对燃烧室喷嘴等零件,但效果不佳、耗时长、能耗高费时费力;超声波清洗方法可去除一些发动机较小的零部件,同时超声波清洗过程时间长,清洗需要完全拆解整个部件,无法直接在线清洗。 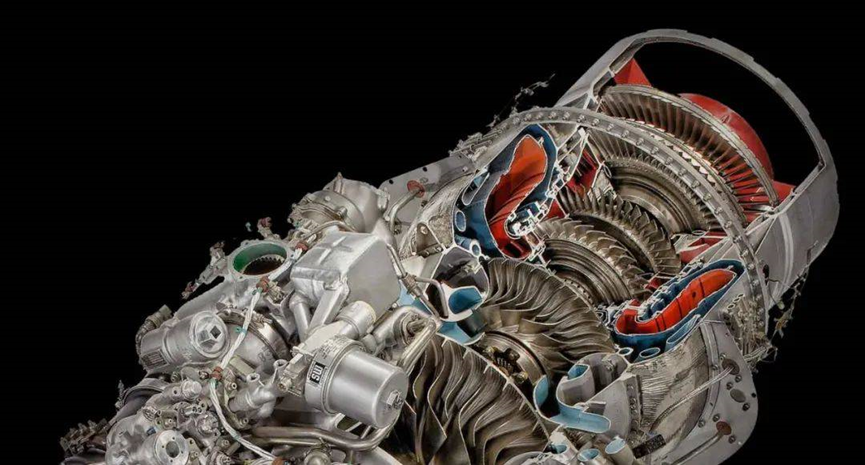
图源:普惠 传统的飞机发动机清洗方法功能单一、设备昂贵能耗高、清洗耗时长和清洁度不高等缺点。而在军工、电力行业及轨道交通领域广泛应用的干冰清洗技术去除污染物,通用性强且具有良好的环保和经济效益。 突驰科技参与技术研讨,从理论、仿真与试验等方面分析干冰清洗作用机理,开发出适用于飞机发动机零部件清洗的工艺方法,并将该技术应用至航天发动机的维修中。 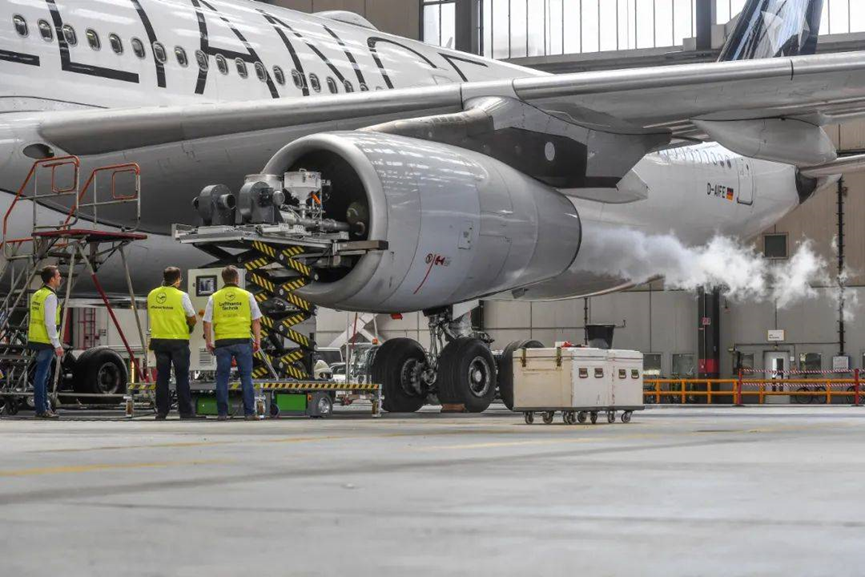
图源:汉莎航空维修车间干冰清洗作业 干冰清洗技术原理剖析 干冰清洗(dry ice blast cleaning)又称干冰冷喷技术,是以压缩空气作为动力和载体,以干冰颗粒为被加速的粒子,通过专用的干冰喷射清洗机喷射到被清洗物体表面,利用高速运动的固体干冰颗粒的动量变化(Δmv)、升华、熔化等能量转换,使被清洗物体表面的污垢、油污、残留杂质等迅速冷冻,从而凝结、脆化、被剥离,且同时随气流清除。不会对被清洗物体表面,特别是金属表面造成任何伤害,也不会影响金属表面的光洁度。 具体清洗过程包括:低温冷冻剥离、吹扫剥离、冲击剥离。 低温冷冻剥离 -78.5℃的干冰颗粒作用在被清洗的物体表面时,首先冷冻脆化污物,污物在被清洗的表面上破裂,由粘弹态变成固态,且脆性增大,粘性减小,使之在表面上的吸附力骤减,同时表面积增大,部分污物可以自动剥离。 吹扫剥离 在压缩空气作为动力的环境下,其对脆化了的污物产生剪切力,引起机械断裂,由于污物与被清洗物表面低温收缩比差很大,在接触面处产生应力集中现象,污物在剪切力作用下剥离。 冲击剥离 高速的干冰颗粒碰撞到增大了的污物表面时,将上述动能传递给污物,克服已经减小了的粘附力,因此而产生的剪切力使污物随气流卷走,达到了脱除污物的目的。 突驰科技利用软件对喷嘴流场及干冰颗粒运动进行仿真分析,基于计算流体动力学进行数值模拟分析,获得气体的速度场、压力场分布情况。干冰微粒喷射过程实际上是一种两相运动,包含干冰颗粒的固相和压缩空气的气流相。在连续的气流相中加入干冰颗粒,将会引起气流的流动状态产生相应影响。使用软件模拟干冰颗粒运动轨迹,可看作是气体和干冰颗粒的气固两相流仿真。由于喷嘴内部和外部压力相差较大,会产生压力波和激波,采用二维模型能够很好地捕捉到轴线附近的压力波动。 分析软件对干冰微粒的运动情况进行模拟仿真。首先待气相流场稳定,然后设置干冰微粒的相关参数,加载可形变部件模型(DPM),待残差收敛后,查看颗粒的运动轨迹及干冰微粒的速度分布情况。 干冰粒经喷枪加速后,在射流空间中先呈聚集状态喷射,然后呈发散状态喷射,模拟喷嘴内部和外部气流流场速度分布云图及对称轴线速度变化曲线如图3所示,云图反映出喷嘴气体速度大小的差异。拉瓦尔喷嘴在出口外产生激波,形成了膨胀波与激波相交和反射的现象,最大速度集中在5~15cm范围内,即干冰清洗常用喷射的距离,此时喷嘴产生的气流依旧能保持较高的速度,喷嘴会有更高的清洗效率。 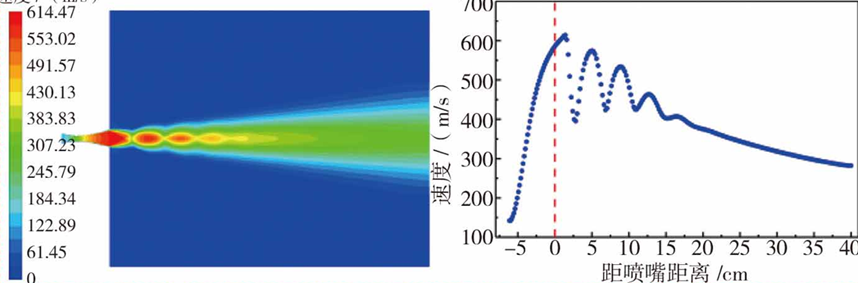
图3. 喷嘴速度与压力分布情况 干冰清洗积炭试验过程中的喷射压力设为0.7MPa,喷射角度为60°,喷射距离为10cm。结果显示,积炭在干冰的撞击下极易脱落,仅需约11s的时间就可以把面积为62cm3的积炭清除干净,清洗效率达95%以上,对比清洗进程图,清洗前后效果明显。 受清洗材料分析 突驰科技研发团队针对航空行业常用材料 2024-T3 铝合金进行干冰实验测试。铝的表面涂有几微米厚的铝保护层(称为复合合金)。这是一种常见的航空合金材料,这种材料比合金具有更好的耐腐蚀性,并且保留了合金本身的机械性能。为了比较,我们采用了碱性化学清洗和酸性清洗的工艺加入对比,其中实验条件是根据制造商的说明选择的。因此,对三种类型的样品进行了分析:a) 未经预处理的未清洁基础合金,b) 化学清洁合金,以及 c) 用干冰清洁的合金。测量2-D和3-D表面形貌,用扫描电子显微镜记录表面形貌,并使用能量色散X射线光谱进行基本化学分析。 图 4 显示了 3-D 表面形貌的比较,以及粗糙度值 (Ra )。干冰清洗过程对表面无创,因此粗糙度与清洗前的表面相当。相比之下,化学清洗对铝和合金的保护层更具侵略性,因此表面更粗糙,天然保护层被破坏或去除。 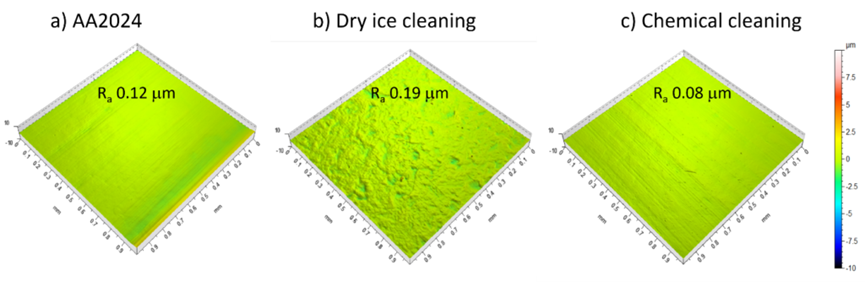
图 4:2024-T3 复合铝合金表面形貌的 3D 显示:(a) 未清洁的表面,(b) 用干冰清洁,和 (c) 化学清洁。图中提供了粗糙度值 (Ra)。 扫描电子显微镜图像显示未清洁样品表面存在杂质(暗斑),并且还可见金属间夹杂物(轻颗粒)。后者含有铁、铜、硅等(图5)。因此,金属间化合物在化学上与基体表面不同,在这种情况下,基体表面是铝层,其下方是 2024-T3 基合金。还给出了记录在基质或不同夹杂物上的元素组成光谱。干冰预处理过程去除了杂质,同时保持了铝包覆基体的形态。金属间化合物的数量仍与未清洁表面上的相似。相比之下, 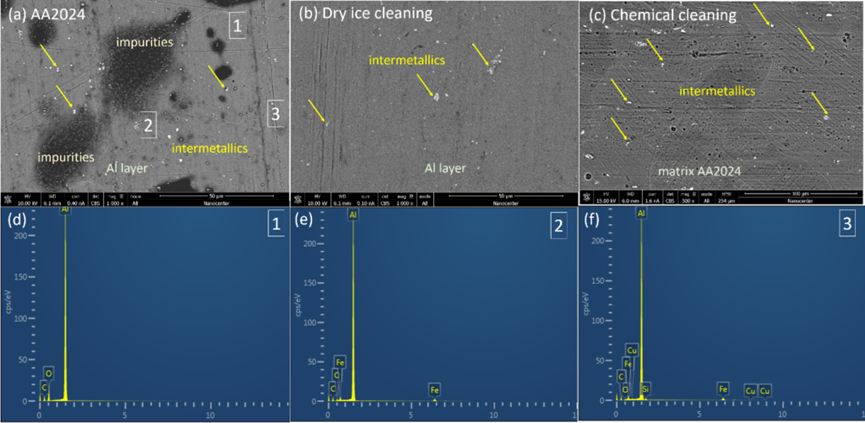
图 5:用扫描电子显微镜拍摄的 2024-T3 复合铝合金的表面图像和化学分析:(a) 未清洁的表面,(b) 用干冰清洁,和 (c) 化学清洁。图像中突出显示了杂质、金属间化合物(黄色箭头)和基底(Al 涂层或 AA2024 基体)。图 (d)-(f) 显示了以下化学成分的 EDS 光谱:(d) 铝涂层,(e) 和 (f) 含铁和铜的金属间化合物。EDS 光谱已记录在点 (1, 2, 3),如图 (a) 所示。 接下来,使用标准盐雾室腐蚀试验在 35°C 和 5 wt% 氯化钠下测试样品的耐腐蚀性。图 6 显示了 24 小时暴露前后的样品表面。虽然在未清洁和化学清洁的表面上已经观察到腐蚀损伤和腐蚀表面产物,但用干冰清洁的表面仍然没有任何腐蚀迹象。 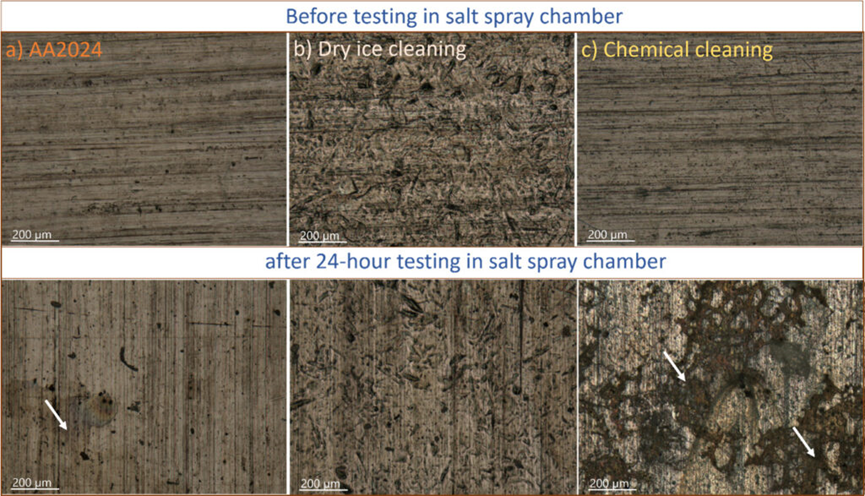
图 6:2024-T3 复合铝合金在腐蚀室内暴露于盐雾 24 小时前后的表面图像(37°C 和 5 wt% NaCl):(a)未清洁表面,(b)清洁用干冰,和 (c) 化学清洗。腐蚀产物标有箭头。 根据此处提供的结果,用干冰清洁金属表面是化学清洁的可行替代方案。由于干冰表面清洁过程是非侵入性的,它不会去除 2024-T3 铝合金上的铝覆层——因此保留了腐蚀特性。相比之下,化学工艺去除了保护性氧化层,从而显着降低了合金的腐蚀保护能力。当然,关键区别在于干冰应用过程的对于环境的可接受性,因为该过程不使用化学清洁剂并且快速且经济。初步研究表明,用干冰清洁的表面可以实现转化涂层的均匀和保护性应用,这实际上是进一步研究的主题。 根据仿真、试验及材料属性分析可知,干冰清洗技术积炭清除效果好,且对材料无影响。突驰科技对发动机零部件进行了干冰清洗积炭实际应用验证,清洗前后对比效果明显,同时对各零部件目视检查,表面均无明显损伤 干冰清洗技术具有环保,高效率等优点,能够实现单件或装配在线状态下组件复杂空间的清洗作业,大大提高了清洗效率,极强的通用性强,在清洗航空发动机零组件积炭具有良好的应用前景。相对于高温、化学与手动清洁,该技术大大降低了生产耗能,同时极大地缩短了零部件积炭清洗周期,节省了排故周转时间,提升了生产效率。 参考文献 [1] 黄艳斐, 朱岳麟, 熊常健,等. 航空发动机喷嘴结焦积炭的性质[J]. 北京航空航天大学学报, 2011(06):126-129. [2] 王旭全. 积炭对发动机性能的影响[J]. 黑龙江交通科技, 2008, 31(5). [3] 李晓东, 刘传绍. 超声波清洗技术的研究与应用现状[J]. 清洗世界, 2009, 25(1). [4] 黄艳松. 某发动机导向叶片表面积炭去除工艺研究[J]. 机械工程师, 2015(11):77-79. [5] 武爽爽,贾秀杰,熊胜.面向再制造的油漆清洗技术综述[J].表面技术,2021(3):51-65. [6] 吕平.干冰微粒喷射技术综述[J].真空科学与技术学报,2016(8):112-118. [7] 段学明.干冰清洗技术在汽车行业的应用[J].清洗世界,2006(11):9-11. [8] 李烨,谭昭怡,张东,等.干冰喷射去除表面放射性污染技术研究[J].辐射防护,2018(2):57-62. [9] 许娟红,火巧英,王国平. 干冰清洗技术在轨道车辆中的可行性分析[J]. 中国设备工程,2020(12):173-174. [10] 郑建林 王友涛 栗娜娜 汪祥 宋金龙 Dry Ice Jet Technology for Aero Engine Carbon Deposition Washing [11] Prof. Dr. Ingrid Milošev Cleaning metal surfaces with dry ice as an alternative to chemical cleaning [12] A.S. Warren, Materials Forum, 28 (2004) 24-31, editors J.F. Nie, A. J. Morton, and B.C. Muddle, Institute of Materials Engineering Australasia Ltd. [13] M. Doerre, L. Hibbitts, G. Patrick, N.K. Akafuah, Coatings, 8 (2018) 405 [14] I. Milošev, Acta Chimica Slovenica, 66 (2019) 511-533
|